Dust in the air is now 'negligible' in the bag loading area making it much safer for staff.
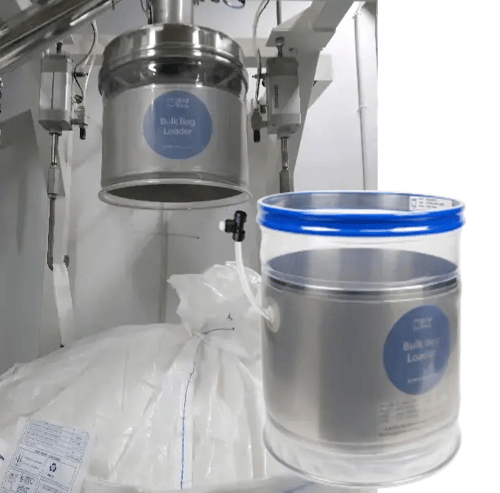
A UK-based monolithic refractory manufacturer that produces over 300 products was particularly concerned with the dust generated during their bulk bag loading process.
The products being handled included raw materials such as sand, lime and dolomite, all of which potentially contain respirable crystalline silica (RCS), which can cause serious respiratory diseases with long-term exposure.
After trialling a range of different solutions, they found none were durable or effective enough - until they found the BFM® fitting Bulk Bag Loader!
The company fills around 60 bulk bags daily, transferring materials from silos into bags that are then transported for mixing. The existing clamp system used to secure the bags during filling was proving inadequate, allowing dust to escape during the process. As the materials handled pose an RCS risk,, effective dust containment was not only a priority—it was essential.
Despite having local exhaust ventilation (LEV) systems and both static and personal dust monitors in place, the site struggled to control dust leakage at the point where the bulk bags connected to the filling head.
The engineering team trialled a range of different solutions, including inflatable seals, but these options fell short, either due to insufficient dust reduction or premature wear and tear. It was clear they needed a more durable, effective solution.
Local BFM® fitting Authorized Distributor, ProSpare Ltd, recommended installing two BFM® Bulk Bag Loaders to control the dust and improve the overall efficiency of the bag loading stations.
Dust emissions during the filling process have dropped dramatically, limiting the risk of exposure to RCS. Rigorous on-site testing by the engineering team, along with external audits, confirmed that dust levels in areas where the BFM® Bulk Bag Loader is in use are now considered ‘negligible.’
In addition to the impressive dust control, the team at the site has praised the durability of the BFM® Bulk Bag Loader. After more than two and a half years of daily use, the loaders show no signs of wear. This resilience, particularly in the stainless-steel core and urethane material, ensures long-lasting performance, even under continuous operation.
Dust in the air is now 'negligible' in the bag loading area making it much safer for staff.
“The BFM® Bulk Bag Loader is a Godsend and the only option on the market that works for us when filling.”
- Director of Engineering
Case Study provided courtesy of BFM® Distributor ProSpare Limited (United Kingdom)
Our most popular connector that can be used in virtually all applications. Made from clear ether-based thermoplastic polyurethane alloy.
A 100% polyester needle-felt breather bag designed for breathing applications such as venting hoppers, sifters and other contained vessels.
We have Authorized Distributors who will help work through what you want to achieve and how BFM® fitting can improve your plant.
The canvas weigh hopper connectors at a leading British concrete products manufacturer absorbed moisture, making them prone to blockages. This caused...
BFM® fitting is transforming processing plants globally. Keep updated on news, products, insights and new product developments.