The financial and reputational damage that can be caused by industrial accidents has seen rapid change in both regulations and attitudes to safety in recent years.The emphasis on risk mitigation and worker protection means you need to be seen to be doing everything you can to reduce potential harm to staff and their exposure to hazardous environments.
Anyone working in the bulk handling of dry products knows that processing any powders is relatively high-risk and therefore complying with safe powder handling practices is important.
And whilst we all want to do the best for our staff, regulatory health and safety compliance often comes at a significant cost to your business. So how can manufacturers who process powders reduce both risk to their staff and their ongoing compliance costs?
Dust Control & Proper Maintenance
Powder processing is high risk mainly because of the potential for electrostatic build-up and the possibility of secondary explosions. These can occur when there is an explosion in your plant or equipment, and any dust on surfaces outside of the machinery becomes airborne due to the shock of the primary blast. This dust cloud can then ignite, causing a more devastating, secondary explosion.
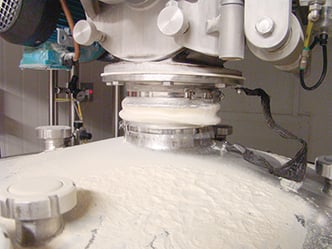
The number one overall priority for preventing secondary explosions is therefore reducing the amount of dust present outside of your processing equipment.
That means it’s vital to ensure that any flexible connections between your equipment are strong, durable and will contain your product 100% so dust can’t escape your process in the first place.
This will not only reduce your explosion risk, but it will help lower your ongoing cleaning costs and any potential unplanned downtime for spills and leaks due to torn or ill-fitting connectors.
The next most important priority to reduce secondary explosion risk is eliminating any possible sources of ignition. Regular preventative maintenance programmes should be undertaken to keep all machinery adequately monitored and cleaned to help prevent any potential for sparking during operation.
Machinery Transitions are a High-Risk Explosion Area
Non-metal transitions between machinery where there is product flow, such as flexible connections, also present an ignition risk due to static electricity, which can build up and lead to spark discharges.Adequate grounding procedures above and below your flexible connections, along with the use of static dissipative materials, like BFM® fitting’s Seeflex range of urethanes, are highly recommended to help reduce the risk of spark discharges occurring in the first place.
If a spark does occur for any reason, it’s important to contain any initial explosion within the machinery itself to ensure you reduce the risk of secondary explosions and injury to staff. The weakest point for the potential escape of these explosive flames and gases is often at the transitions, between machinery.
Traditional hose-clamped flexible connectors tend to give way quickly allowing the explosion to propagate, potentially leading to a deadly secondary explosion.
Choosing a strong, dust-proof and explosion-resistant connector like the BFM® fitting is fundamental to both preventing and containing any explosions that might occur within a process line.
Regulatory Compliant Equipment Can Be Costly
But even with explosion-resistant, dust-proof connectors made from static dissipative materials, international safety regulations like ATEX and IECEx can also require that any electrical equipment within a certain radius of a flexible connection needs to be ‘rated’ to comply with that regulation’s standards.
Within the ATEX framework, for example, factory areas are classified into explosion risk ‘zones’ and these must be protected from any possible sources of ignition. This means that all equipment and protective systems intended to be used in these zone areas must also be ATEX compliant.
This is in case there is a failure of a process equipment component, like the flexible connector, and dust escapes into the immediate environment. That event would be potentially setting the scene for a combustible dust explosion if a spark were to be created by the electrical equipment in that zone.
The issue with this explosion zoning from a compliance-cost perspective is that ATEX-rated equipment can be substantially more expensive than standard versions, simply because of the nature of the additional casing and sealing required to achieve the certification.
Reduce Your ATEX zones with BFM® fitting
A number of BFM® fitting customers have addressed this challenge by installing a double layer of BFM® fittings on potential high-risk transitions. If the inner connector was to fail for any reason, the outer connector would immediately contain any dust from escaping into the rest of the factory.
This effectively means the ATEX safety risk zone is now just the space in-between the two connectors, thus reducing the entire outer factory environment’s ATEX zoning risk.
This simple solution has saved these customers thousands in electrical equipment costs as they weren’t required to install the higher-specification (and higher priced) ATEX-rated equipment.
BFM®’s Seeflex range of connectors are already approved for use in ATEX explosion zones, and this additional option is an excellent way to maximise the benefits of your investment in a BFM® fitting system.
Find out more about how BFM® fitting system helps make your plant safer.