Product recalls would be high on the list of most manufacturing businesses ‘worst-case' scenarios. They can severely impact any manufacturing business, particularly in the food processing industry. Not only can contamination issues result in significant financial losses, but they can also cause lasting reputational harm.
The Financial Impact of Product Recalls
According to a study by the Food Marketing Institute and the Grocery Manufacturer’s Association, the average direct cost of a product recall is US$10m. Besides the immediate expenses associated with removing contaminated products from the market, recalls often necessitate disposing of large product quantities, conducting comprehensive investigations, and implementing corrective actions.
In severe cases, recalls might also lead to legal fees, government fines, and lost revenue from halted production lines.
This ripple effect can lead to millions in losses.
Reputational Damage and Long-Term Consequences
Beyond financial losses, the damage to a company’s reputation of a product recall can be irreparable.
Consumers are increasingly aware of food safety standards, and a single contamination incident can significantly impact customer trust and brand loyalty.
News of recalls due to contamination often spreads widely, especially online, creating a negative perception that can take years to mend. Loss of consumer confidence may even lead to losing key clients, especially if the issue becomes widespread.
Contamination is a persistent threat in manufacturing, particularly when certain types of equipment are used. One of the highest-risk locations is the transition points between machinery where product flows through a flexible connection of some sort.
Why Flexible Connections Can Be A Serious Contamination Risk
Flexible connectors need to be attached to different pieces of equipment, which presents challenges in keeping the connection sealed, secure and hygienic at all times.
When movement and pressure are added to the mix, the potential for connector failure and product contamination is heightened considerably.
Bacterial Build-up In Connector Crevices
Old-style clamped flexible connectors sit on the outside of pipes and create significant crevices that are highly prone to contamination. Gaps between connector materials and piping create spaces where food particles can easily get trapped (see example adjacent).
This is very common when there is positive pressure inside a process line. Fine powdered product is effectively pushed outwards and forced between the small gaps.
In warm processing environments, bacteria can quickly multiply in these areas, increasing the risk of contamination. Should any of this trapped material enter the production line, entire batches can become tainted, rendering them unfit for sale.
Contamination from External Sources
In food processing plants, areas of low pressure often allow contaminants to enter the system under vacuum. Clamped connectors generally have a poor seal, which can pull dust or other airborne contaminants into the process, threatening product integrity.
This introduction of contaminants from outside the process line can easily go undetected.
Other common causes of contamination involve the physical clamping mechanisms themselves. If a connector fails and needs to be replaced, it is surprisingly common for clamp components such as screws and gaskets to accidentally be dropped into the pipes and vessels below, meaning all product in the line at the time can be contaminated.
BFM® Connectors Help Prevent Contamination
The industry-leading BFM® flexible connector system offers an extremely versatile and hygienic solution to help prevent product contamination. This is because of its unique, internally snap-fitted design that creates smooth internal surfaces and provides a superior seal under both positive and negative pressure.
Because they seal from the inside, the design of the BFM® connectors prevents the buildup of harmful bacteria, ensuring that production remains hygienic and contamination-free.
BFM® fittings don’t use clamps of any kind, which means there is no risk of any components falling into the production line if a connector needs to be removed or replaced.
Additionally, BFM® connectors are compatible with Clean-In-Place (CIP) and Clean-Out-of-Place (COP) applications, allowing for thorough, regular cleaning without fully dismantling machinery. This reduces downtime, maintaining productivity while ensuring high hygiene standards.
In the case of process lines under vacuum, the superior seal of the BLUEBAND™ flexible connector cuff and spigot system means that no air can be sucked in from the outside, protecting the purity of the product inside.
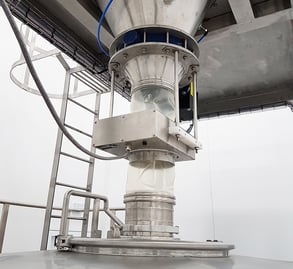
Enhanced Product Safety with Metal Detection Integration
The use of metal detectors is essential in food manufacturing to prevent any kind of metal contamination from reaching consumers.
BFM® connectors integrate smoothly with metal detectors, helping ensure product safety and quality. Connectors are easily fed through the metal detector when installing and are fast and easy to clean and change when necessary. Plastic rings can also be inserted for longer drops to ensure the aperture of the connector is kept open for optimal product flow.
Additionally, BFM® offers Quick Access Ports on its connectors (shown adjacent) for inserting test balls or taking samples, minimizing the chance of contamination while maintaining rigorous safety checks.
Global Certifications for BFM® Connectors
Hygienic design and strict quality controls have seen BFM® fitting’s connectors certified by multiple regulatory agencies, including the FDA, USDA, and 3-A in the U.S., EC in Europe, and more recently, Chinese certification as well.
These certifications underscore the commitment to food safety and regulatory compliance across global markets, making BFM® a trusted solution for multinational companies.
Choose BFM® fitting to Help Minimise Contamination Risk Factors
A product recall's financial and reputational consequences are severe, with costs extending far beyond the recall itself. By implementing BFM® connectors, manufacturers can significantly reduce the risk of contamination.
Through their crevice-free, airtight design and compatibility with rigorous hygiene standards, BFM® systems ensure the highest levels of product integrity and help protect a company’s reputation and bottom line.
Find out more about how the BFM® fitting system helps keep your plant hygienically clean.